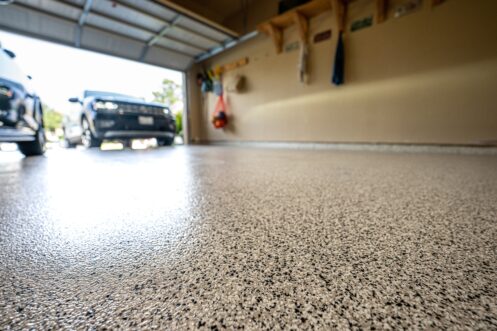
Floor coatings offer a protective and aesthetically pleasing update for any space, whether it’s a basement, garage or business. However, there are a lot of moving parts when it comes to estimating the cost of a floor coating project. Having a comprehensive grasp of all these factors, including material selection, labor and long-term maintenance, will enable you to create a realistic budget and steer clear of unforeseen costs.
Types of Floor Coatings and Their Costs
Make sure to consider both the initial investment and the expected ROI when choosing a floor coating. Although higher-quality coatings initially cost more, they end up saving you money due to their long lifespan and minimal maintenance needs. Every one of the most common floor coating options — epoxy, polyurethane, polyaspartic and acrylic — has its own quirks, advantages and price points.
For instance, epoxy coatings can withstand a lot of wear and tear without succumbing to chemicals or abrasions. The most expensive coating choices, such as metallic epoxy or flake systems, can cost anywhere from $3 to $12 per square foot. Outdoor applications frequently make use of polyurethane coatings due to their increased flexibility and resilience to ultraviolet light. The price per square foot for these coatings usually ranges from $4 to $8.
For commercial areas that need minimum downtime, a newer option known for fast curing times — poly aspartic coatings — can be a great fit, costing anywhere from $7 to $12 per square foot. Lastly, acrylic coatings are less expensive, around $1 to $3 per square foot, but they aren’t as long-lasting and can require more regular repairs.
Labor Costs: What to Expect
The majority (40% to 60%) of the money you’ll spend on your floor coating process will go toward labor expenses. Hourly rates for a professional to coat the floors of a typical basement or garage may range from $3 to $8 per square foot. Coating application, surface preparation and cleanup after installation are all part of the process. The time and skill needed to complete a project with elaborate designs, artistic finishes or custom branding can drive up the cost of labor.
Surface Preparation and Its Impact on Costs
To avoid problems like bubbling, peeling or early wear, it is crucial to prepare the surface properly. If you skip or cut corners at this stage, you can end up spending more money fixing it or applying it again. The overall cost of the project can increase by $1 to $2 per square foot for basic surface prep, which usually consists of cleaning and light sanding; this assumes your floor is in good condition. More thorough preparation, such as shot blasting, grinding or crack filling, may be necessary if your floor has stains, cracks or moisture issues. Prices can go up to $3 or $4/sq. ft. due to the more extensive preparation required.
DIY vs. Professional Installation: Cost Differences
Choosing to tackle this project yourself can help you save a ton of money on labor — anywhere from 40% to 60% off the total cost. Still, there are obstacles to overcome when installing on your own. The cost of specialized equipment, such as grinders or applicators, can range from $200 to $500, depending on whether you rent or buy them. More expenses may arise in the future as a result of improper application or surface preparation.
Professional installation, on the other hand, is usually more expensive up front, but it comes with a warranty, expert knowledge and peace of mind. Prices for professional installation can vary from $1,500 to $4,000 per garage, with DIY kits costing $200 to $500 for a typical two-car garage.
Geographical Location and Pricing Variations
The price tag for your floor coating project could change depending on where you live. Labor costs tend to be higher in places like major urban regions, where there is a greater demand for trained workers. Material costs can also change depending on what’s readily available where you live. You could get better deals in less populated areas or in places where there are fewer contractors. If you want to know how much things cost in your area and whether you’re getting a good deal, it’s a good idea to look into the market there and get estimates from several contractors.
Estimating Long-Term Maintenance Expenses
Although floor coatings typically require little upkeep, certain expenses may come up in the long run. Depending on the amount of wear and tear they suffer, coatings like epoxy or polyurethane may require touch-ups every five to 10 years. Maintenance expenses might vary from $500 to $2,000, depending on the repairs needed. To keep these costs to a minimum, you should keep your coated floor clean, fix small cracks or damage right away and check for moisture to make sure the coating isn’t deteriorating.
Budgeting for Unexpected Costs
Unanticipated expenses could crop up during your floor coating process, no matter how well you prepare. You might end up spending more than you planned due to issues like unexpected floor damage, moisture issues or last-minute adjustments to the coating you originally chose. A smart decision to allocate an extra 10% to 20% of your total expected cost to account for any unforeseen circumstances that may arise throughout the project. This will help you stay within your budget.
Maximizing Value While Reducing Costs
Choosing the most affordable option won’t always result in the best floor coating for your project. The emphasis should instead be on picking reliable, high-quality materials that will last. To avoid expensive repairs down the road, it’s a good idea to invest in surface preparation and think about hiring a professional installer for more complicated tasks. Many homeowners find they can save money by putting less expensive coatings, like acrylic, in low-traffic areas and saving the more expensive ones for rooms that get the most traffic.
How the Number of Coatings Affects the Final Price
In floor coating projects, the total cost is proportional to the number of coats applied. Primers, base coats and topcoats all add more work and materials to the project. Although it may be more economical to apply a single layer, you may end up saving money on maintenance by using a multi-layer coating due to its increased resilience and lifetime.
Floor Coating Alternatives
There are a number of long-lasting and aesthetically pleasing alternatives to common floor coverings like epoxy and polyurethane. Polished concrete is one option; it gives concrete surfaces a beautiful sheen and lasts a long time without requiring any care. Rubber flooring is a popular choice because it provides cushioning and is resistant to slips, making it ideal for playgrounds and fitness centers. Vinyl flooring is a low-maintenance, low-cost alternative to more expensive materials like wood or stone. Last but not least, if you’re looking for a solution that is both long-lasting and resistant to moisture, consider tile or stone for your kitchen or bathroom.
If you have questions about floor coatings, Valley Concrete Coatings & Polishing has the answers. We have unique color charts that you can use to pick the perfect coating. We also offer cool decking, concrete staining and concrete floor restoration. Call us now to schedule a floor coating project for your home with one of the best floor companies in Phoenix, AZ.
